单螺杆造粒机的螺杆一般分为加料段、压缩段和均化段。在加料段,螺杆底径较小,其主要任务是将原料平稳输送至后续阶段。螺槽深度 h1 通常为 (0.12 - 0.14) D(D 为螺杆直径),螺旋升角 φ 一般取 17°40′,以满足不同物料的输送需求。进入压缩段,螺杆底径逐渐变化,螺槽深度变浅,对物料进行压实、熔融,并建立压力。压缩比 ε(ε=h1/h3,h3 为均化段螺槽深度)和长度 L2 是关键参数,精确的参数设置能保证物料充分熔融和压实。均化段将压缩段已熔物料定量定温地挤到螺杆前端,此段螺槽深度 h3 一般为 (0.05 - 0.07) D ,进一步均匀塑化物料,稳定压力和温度,为机头挤出提供质量稳定的物料。蒸汽加热适用于对温度稳定性要求较高的造粒工艺。安徽双螺杆造粒机保养
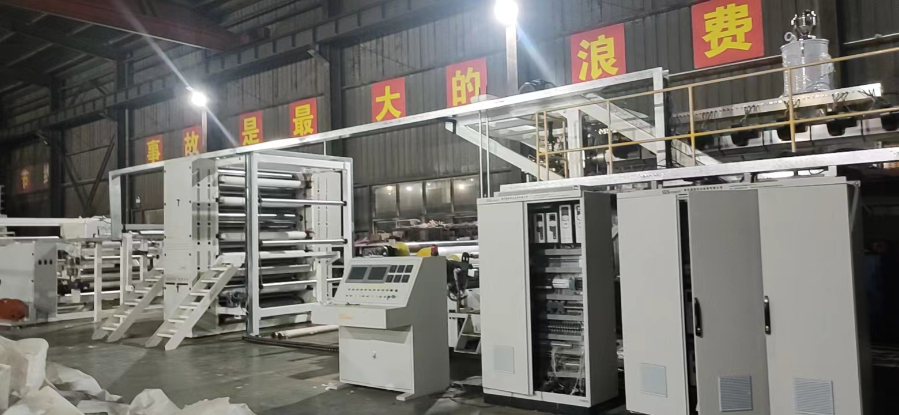
主机料筒的温度控制对单螺杆造粒质量起着关键作用。采用电加热、水冷却自动控制机筒温度的方式,可根据不同原料特性和生产要求精确调节温度。不同塑料原料,如 PP、PE、PS 等,其适宜加工温度各异。通过温度控制系统,实时监测机筒温度,并依据设定值自动调整加热功率或冷却水量,确保物料在各加工阶段都处于合适温度环境,实现高效塑化和挤出。例如,加工 PP 时,机筒温度一般控制在 180 - 220℃;加工 PE 时,温度控制在 160 - 200℃,以保证物料充分熔融且不发生分解等异常情况。湖北色母粒造粒机性价比经过造粒后的物料,其堆积密度增加,占用空间减小,降低了储存和运输成本。
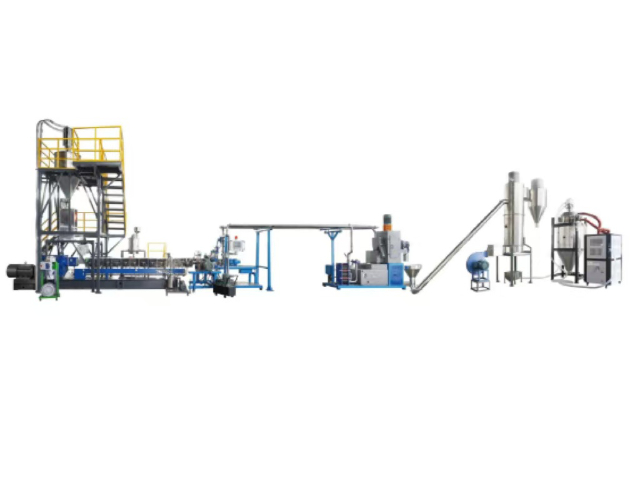
机头成型与切粒工艺是将塑化后的物料转化为成品颗粒的关键步骤,直接决定产品的外观和规格。机头作为关键部件,由合金钢内套和碳素钢外套组成,内装有成型模具。其作用是将旋转运动的塑料熔体转变为平行直线运动,均匀平稳地导入模套,并赋予塑料必要的成型压力 。塑料在机筒内经过充分塑化压实后,经多孔滤板沿一定流道通过机头脖颈流入机头成型模具。模芯模套适当配合,形成截面不断减小的环形空隙,使塑料熔体在压力作用下,在芯线周围形成连续密实的管状包覆层,实现产品成型。为保证机头内塑料流道合理,消除积存塑料的死角,往往安置分流套筒;为消除塑料挤出时压力波动,也会设置均压环,确保成型质量稳定。物料从机头挤出后,需进行切粒。常见的切粒方式有风冷模面热切和水拉条切粒。风冷模面热切适用于多种塑料物料的造粒,旋转刀片由交流电机驱动,通过变频调速实现对切粒速度的精确控制。在切粒过程中,高速旋转的刀片将条料切成均匀的颗粒,同时利用风冷系统对颗粒进行快速冷却,使颗粒迅速定型,避免粘连。水拉条切粒则适用于填充在 50% 以下的物料,物料挤出后通过水槽冷却,再由切刀切成颗粒,这种方式生产的颗粒形状规整,表面光滑。
螺杆在单螺杆生产工艺里承担着重要职责,其独特的结构和精确的参数设定,是实现物料高效输送与完美塑化的关键。螺杆通常分为加料段、压缩段和均化段。加料段底径较小,主要功能是将原料平稳输送至后续阶段。其螺槽深度 h1 一般为 (0.12 - 0.14) D(D 为螺杆直径),螺旋升角 φ 常取 17°40′ ,这一参数设定能较好地满足不同物料的输送需求,确保原料顺利进入压缩段。进入压缩段,螺杆底径逐渐变化,螺槽深度变浅,对物料进行压实、熔融,并建立压力。压缩比 ε(ε=h1/h3,h3 为均化段螺槽深度)和长度 L2 是关键参数,它们的精确设置能保证物料充分熔融和压实。在加工聚丙烯(PP)时,通过合理调整压缩比和压缩段长度,可使 PP 原料在该段充分熔融,为均化段的进一步加工做好准备。均化段将压缩段已熔物料定量定温地挤到螺杆前端,此段螺槽深度 h3 一般为 (0.05 - 0.07) D ,进一步均匀塑化物料,稳定压力和温度,为机头挤出提供质量稳定的物料,保障产品的质量和性能。圆盘造粒机工作时,物料在圆盘上滚动,通过喷洒粘结剂等方式逐渐形成颗粒。
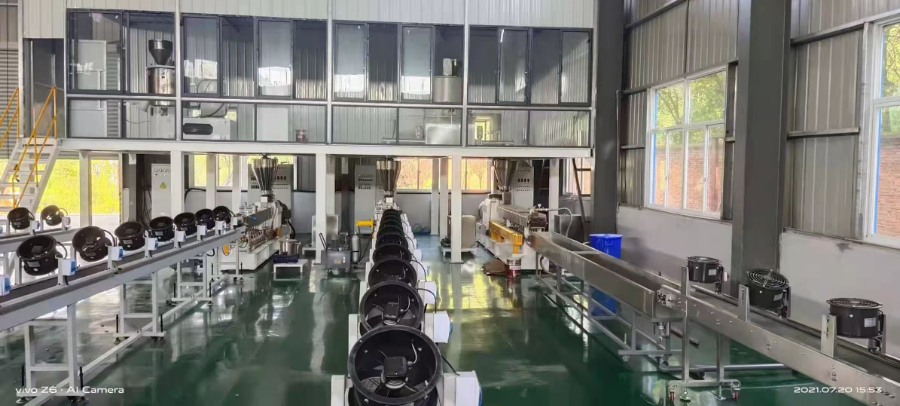
从生产过程来看,双螺杆生产工艺的能源利用效率较高。双螺杆的设计使得物料在机筒内的停留时间更短,塑化效率更高。这意味着在生产相同数量产品时,相比一些传统生产工艺,双螺杆生产能减少能源消耗。例如,在生产塑料颗粒时,其快速且高效的塑化过程,降低了加热系统的工作时长,进而减少了电能的消耗,符合节能减排的环保理念。 在废气排放方面,双螺杆生产工艺也有出色表现。由于其对物料的充分混炼和塑化,减少了因物料塑化不完全而产生的废气排放。同时,先进的双螺杆挤出机配备了高效的废气处理装置,如活性炭吸附装置、催化燃烧装置等,能够对生产过程中产生的少量废气进行有效净化处理,降低有害气体的排放,减少对大气环境的污染。 另外,双螺杆生产工艺在废料回收利用上也发挥着重要作用。在塑料加工过程中,难免会产生一些边角料和不合格产品。双螺杆挤出机可以将这些废料重新混入原料中进行加工,通过再次塑化、混炼,使其成为可再次利用的塑料颗粒,实现资源的循环利用,减少了废料对环境的压力。例如,在生产塑料管材时产生的边角料,经过双螺杆挤出机的处理后,可重新用于管材生产,降低了生产成本,也减少了废弃物的产生 。切粒方式包括水拉条切粒、风冷模面热切、水环切粒和水下切粒等。安徽双螺杆造粒机保养
自动化造粒机能够实时监测和调整生产参数,提高生产效率和产品质量的稳定性。安徽双螺杆造粒机保养
在单螺杆造粒过程中,物料输送贯穿始终。从原料输送到成品颗粒输送,都需要高效、稳定的输送设备。自动提升机将经过预处理的原料输送至双锥喂料机,双锥喂料机再将物料强制均匀加入主机螺杆。切粒后的颗粒通过一级旋风分离器和二级旋风分离器进行初步分离和输送,利用旋风分离器内部的高速旋转气流,使颗粒与空气分离,实现初步的输送和冷却。然后经过加长风冷振动筛进一步筛选和冷却,通过风吹储料仓进行储存和输送,确保生产过程的连续性和高效性。安徽双螺杆造粒机保养
文章来源地址: http://jxjxysb.fzpgjgsb.chanpin818.com/slj/slzlj/deta_28472788.html
免责声明: 本页面所展现的信息及其他相关推荐信息,均来源于其对应的用户,本网对此不承担任何保证责任。如涉及作品内容、 版权和其他问题,请及时与本网联系,我们将核实后进行删除,本网站对此声明具有最终解释权。