真空石墨煅烧炉的微波等离子体复合处理技术:微波等离子体复合处理技术将微波加热与等离子体技术相结合,为石墨表面改性提供了新途径。在真空煅烧过程中,先利用微波对石墨进行快速加热,使其表面活化;然后引入等离子体,等离子体中的活性粒子与石墨表面发生化学反应,实现表面刻蚀、掺杂和涂层沉积等功能。通过调节微波功率、等离子体气体成分和处理时间,可精确控制石墨表面的改性程度。在超级电容器用石墨电极的制备中,采用该技术后,石墨电极的比表面积增加 40%,电解液浸润性提高 35%,电极的充放电性能明显提升,为高性能储能材料的制备提供了创新技术支撑。真空石墨煅烧炉的炉膛尺寸可扩展至直径1m,满足大型航空部件烧结需求。甘肃石墨煅烧炉型号
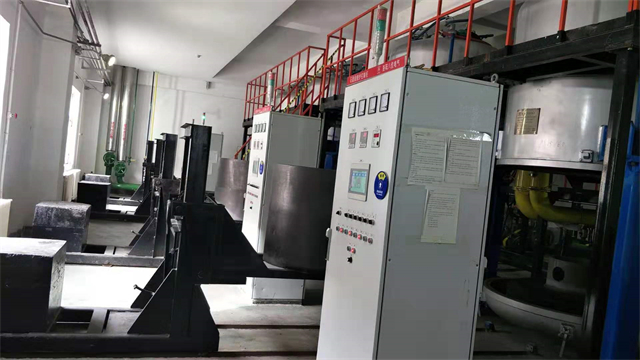
真空石墨煅烧炉的磁屏蔽抗干扰系统:在电磁环境复杂的工业场所,磁屏蔽抗干扰系统保障了真空石墨煅烧炉的稳定运行。该系统采用双层磁屏蔽结构,内层为高导磁率的坡莫合金,可屏蔽低频磁场(50Hz - 1kHz);外层为高电导率的铜网,用于抑制高频电磁场(1MHz - 1GHz)。同时,对炉内的电子控制设备采用电磁兼容设计,所有信号线均采用屏蔽电缆,并安装共模电感和滤波器。在邻近大型变电站的石墨生产车间,安装磁屏蔽抗干扰系统后,炉内温度控制精度从 ±5℃提升至 ±2℃,真空度波动范围从 ±0.5Pa 缩小至 ±0.1Pa,有效避免了电磁干扰对煅烧工艺参数的影响,确保了产品质量的稳定性。甘肃石墨煅烧炉型号哪种石墨原料在真空石墨煅烧炉里,能更快完成结构转化?

真空石墨煅烧炉的仿生纳米涂层抗结焦性能研究:仿生纳米涂层借鉴荷叶表面的超疏水结构,有效解决了石墨煅烧过程中的结焦问题。涂层采用溶胶 - 凝胶法制备,在炉内壁表面形成由二氧化钛纳米颗粒和含氟聚合物组成的复合涂层。纳米颗粒构建粗糙的微纳结构,含氟聚合物降低表面能,使涂层的水接触角达到 155°,具有超疏水性。在石墨煅烧过程中,产生的焦油等有机物难以附着在涂层表面,而是形成液滴滚落。实验表明,涂覆仿生纳米涂层的炉壁,结焦量减少 80%,清洁周期从每周一次延长至每月一次,降低了人工维护成本,同时避免了结焦对炉内温度场和真空度的影响,保证了煅烧工艺的稳定性。
真空石墨煅烧炉的自适应压力调控策略:自适应压力调控策略根据煅烧过程的实时需求动态调整炉内压力。系统通过压力传感器采集炉内压力数据,结合物料的失重率、温度变化等参数,利用模糊控制算法自动调节抽气速率和保护气体流量。在石墨化阶段,当检测到物料失重速率加快时,系统自动增加抽气速率,将真空度从 10⁻³ Pa 提升至 10⁻⁴ Pa,促进杂质气体排出;在保温阶段,适当降低真空度至 10⁻² Pa,减少高温下石墨的挥发损失。该策略使煅烧过程的压力波动范围控制在 ±0.2 Pa,相比固定压力工艺,产品的密度一致性提高 18%,石墨化程度标准差降低 25%,提升了产品质量稳定性。真空石墨煅烧炉的出现,为石墨深加工带来新方式。
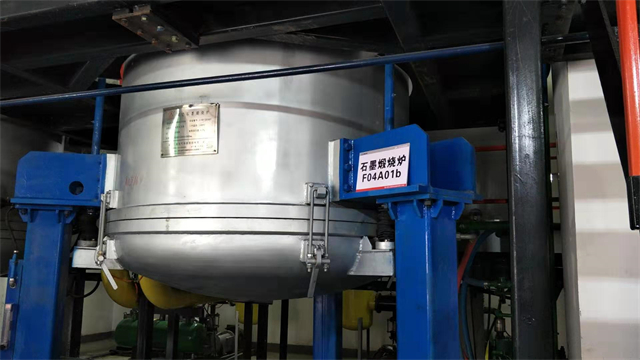
真空石墨煅烧炉的低温余热驱动制冷系统:利用真空石墨煅烧炉的低温余热(100 - 200℃)驱动吸收式制冷系统,实现能源的梯级利用。采用溴化锂 - 水吸收式制冷机组,将煅烧冷却阶段的余热作为驱动热源,制取 7℃的冷冻水。在夏季高温环境下,冷冻水用于冷却真空泵的润滑油和电气控制柜,使设备运行温度降低 10℃,延长设备使用寿命。同时,制冷系统产生的高温冷却水(50 - 60℃)可用于预热原料,形成余热回收的循环链条。在石墨生产车间应用该系统后,每年可减少机械制冷设备的用电量 30 万 kWh,余热利用率提高至 65%,降低了企业的综合能耗。真空石墨煅烧炉的电极采用钼镧合金,使用寿命达2000小时以上,维护成本低。甘肃石墨煅烧炉型号
真空石墨煅烧炉处理后的石墨,在润滑领域有何新应用?甘肃石墨煅烧炉型号
真空石墨煅烧炉的智能机械臂装料系统:智能机械臂装料系统提高了真空煅烧炉的自动化程度与装料精度。机械臂配备视觉识别系统,通过工业相机扫描石墨物料的形状与尺寸,结合预设装料方案,规划装料路径。采用真空吸附式抓手,可准确抓取不同规格的石墨制品,定位精度达 ±1mm。在装料过程中,机械臂根据炉内温度场分布,将物料均匀布置在不同区域,避免因装料不均导致的温度偏差。该系统使单批次装料时间从人工操作的 20 分钟缩短至 5 分钟,同时减少了因人工装料不当造成的产品缺陷,产品一致性提高 18%。甘肃石墨煅烧炉型号
文章来源地址: http://jxjxysb.fzpgjgsb.chanpin818.com/zzjrclsbfg/gongyeluyu/deta_28794730.html
免责声明: 本页面所展现的信息及其他相关推荐信息,均来源于其对应的用户,本网对此不承担任何保证责任。如涉及作品内容、 版权和其他问题,请及时与本网联系,我们将核实后进行删除,本网站对此声明具有最终解释权。