轴是机械传动中的重要部件,根据不同的分类标准(如功能、结构、应用场景等),轴可以分为多种类型。以下是常见的分类方式及其具体类型:一、按功能与受力分类转轴特点:既承受扭矩(传递动力),又承受弯矩(支撑旋转部件)。应用:电机主轴、减速器输出轴、机床主轴等。传动轴特点:主要传递扭矩,弯矩较小,通常为长杆结构。应用:汽车传动轴、船舶推进轴、风力发电机主轴等。心轴特点:承受弯矩,不传递扭矩,分为固定心轴(如自行车前轮轴)和旋转心轴(如滑轮轴)。挠性轴(软轴)特点:由多层钢丝缠绕而成,可弯曲传递动力。应用:手持工具(如牙科钻头)、复杂空间内的动力传输。二、按结构形式分类直轴实心轴:最常见的轴类型,如电机轴、齿轮轴。空心轴:减轻重量且能通过其他部件(如光缆、液压管路),用于航空航天、机器人等领域。曲轴特点:带有曲柄结构,将往复运动转换为旋转运动(或反向)。应用:内燃机曲轴、压缩机曲轴。阶梯轴特点:轴径分段变化,便于安装轴承、齿轮等零件,如减速器中的多级轴。花键轴特点:表面有纵向键槽,与花键套配合传递大扭矩。应用:机床进给系统、汽车变速箱。 雾面辊的工艺流程2表面处理抛光与电镀对辊坯进行抛光处理使其达到镜面效果进行电镀提高表面硬度和耐腐性。通州区压延轴
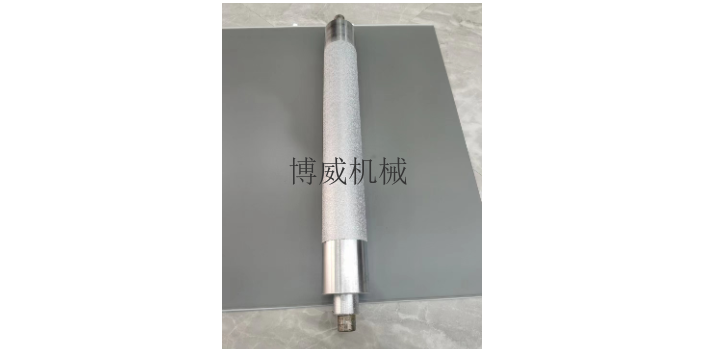
5.现代主轴的重要功能与定义经过长期演变,“主轴”一词已特指机械系统中承担以下重要任务的旋转轴:动力传输:将电机或发动机的动力传递至执行部件(如刀ju、工件)。精密定wei:通过轴承和操控系统实现高精度旋转(如纳米级加工)。承载复合载荷:同时承受扭矩、弯矩、轴向力及振动。6.未来趋势:智能化与绿色制造智能主轴:集成传感器实时监测温度、振动、负载,通过AI优化加工参数。超高速加工:碳纤维复合材料主轴、低温冷却技术突破转速极限。可持续设计:轻量化、低能耗主轴减少资源消耗。总结:主轴演进的逻辑主轴的演变本质是人类对旋转动力操控的不断升级:从人力驱动(陶轮)到自然力驱动(水车),再到蒸汽/电力驱动;从木质粗加工到金属精密化,终实现智能化操控;每一次技术革新(如轴承、材料、数控)都推动了主轴性能的跨越。如今,主轴已成为高尚制造、机器人、新能源汽车等领域的重要部件,其发展史堪称一部浓缩的“机械文明进化史”。 怀柔区镜面轴制造雾面辊注意事项4防火防爆: 使用防爆设备,防止静电或火花引发(baozha)。
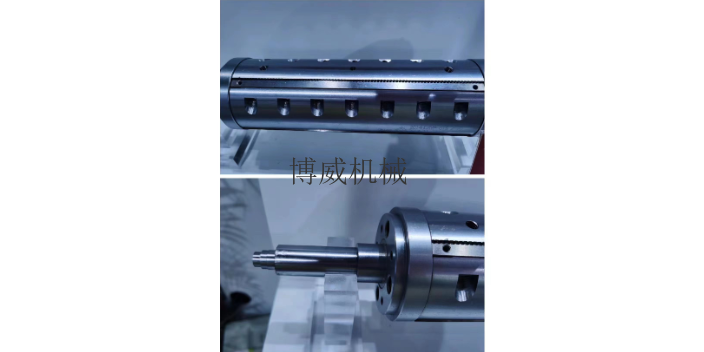
印刷胶辊的使用周期受多种因素影响,通常需结合材质、使用环境、保养情况以及具体工艺要求综合判断。以下是关键信息总结:1.常规使用寿命一般周期:印刷胶辊的平均使用寿命通常为1-2年。在精心维护和规范使用的情况下,4色胶印机的整套水墨辊寿命可达2年;若使用不当(如频繁更换、安装不规范或保养不足),可能缩短至半年或1年158。材质差异:天然橡胶胶辊:使用寿命约2-3年,但易出现膨胀、老化、掉皮等问题11。合成材料(如聚氨酯):耐磨性更强,寿命可达天然橡胶的3-5倍,且在高温、高湿环境下表现更稳定511。2.更换标准印刷胶辊需定期检查,以下情况需考虑更换:磨损:直径减少10%或厚度减至初始的50%3。表面损伤:如划痕、裂纹、麻眼等,可能导致印刷质量下降18。老化:橡胶因氧化或紫外线照射出现硬化、龟裂38。工艺要求:高速印刷机、高温环境等对胶辊性能要求更高,需缩短更换周期36。
3.交通与车辆工程轨道交通车轴传统车轴(非悬臂结构)直径约100-200mm,长度1-3米;若为悬臂式设计(如某些特殊转向架),尺寸会根据受力优化调整。汽车悬架系统悬臂轴(如操控臂)长度通常为,材料为高强度钢或铝合金,截面形状(工字型、管状)影响刚度和重量。4.航空航天与特殊领域飞机机翼悬臂结构现代客机机翼的悬臂长度可达20-40米(如波音787机翼展约60米),采用碳纤维复合材料减轻重量。航天器展开机构太阳帆板或天线的悬臂轴可能折叠时几米,展开后可达数十米,需极端轻量化(如铝合金或复合材料)。影响悬臂轴尺寸的重要因素载荷类型:承受静载、动载、冲击载荷时,需增加截面尺寸或优化材料。材料性能:高强度钢、钛合金、复合材料可减少尺寸(如碳纤维悬臂梁比钢轻50%以上)。振动与变形限制:长悬臂需考虑挠度(如机床主轴悬伸过长会降低加工精度)。制造工艺:铸造、锻造、3D打印等技术限制小/大可行尺寸。总结悬臂轴的尺寸范围跨度极大,从微米级的精密传感器到百米级的桥梁结构均存在。具体应用中需通过力学仿zhen(如有限元分析)和实验验证确定比较好尺寸。若需进一步精确数据,建议提供具体应用场景(如机器人、建筑、车辆等),以便针对性分析! 涂布辊操作规范流程2. 安装与调试速度设置:根据材料和涂料特性设定合适的涂布速度。
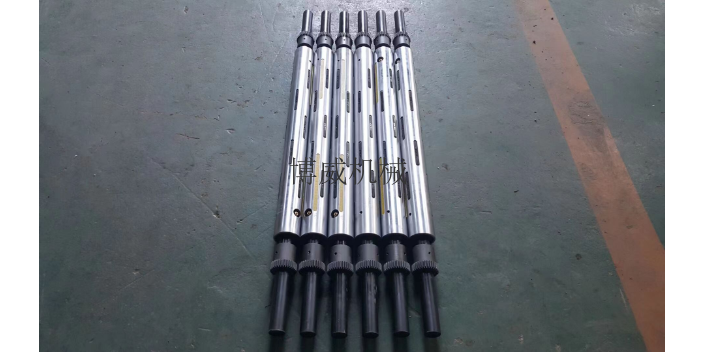
操控难点:多缸同步精度(偏差<2mm),需比例阀+压力补偿器联调。案例2:注塑机合模液压缸工作循环:快su闭模(低压高速)→高ya锁模(高ya低速,压力1000-2000吨)→保压冷却→开模。节能设计:采用变量泵+蓄能器,减少空载能耗(节能30%以上)。六、液压轴的优势与局限性优势:高功率密度:相同体积下输出力远超电动/气动系统(推力可达千吨级)。抗冲击性强:液体不可压缩性天然缓冲负载突变(如挖掘机铲斗撞击岩石)。精细可控:伺服液压系统定wei精度达微米级,动态响应快(毫秒级)。局限性:能耗较高:传统阀控系统效率60-70%(电动系统>90%)。维护复杂:密封件磨损需定期更换,油液清洁度要求高(NAS6级以下)。环境敏感:低温下油液粘度升高,可能影响响应速度。总结与未来趋势液压轴通过压力传递-机械输出-闭环操控的协同,成为重型、高精度场景的重要执行元件。未来发展方向包括:电动液压融合:电动静压驱动(EHA)结合电机与液压优势,提升能效。智能化升级:AI预测性维护(如密封寿命评估)降低停机危害。绿色技术:生wu降解液压油(如HEES型)减少环境污染。选型建议:重载低频场景:优先双作用液压缸+比例阀操控。高频精密操控:伺服液压马达+数字操控器。 钢辊制作工艺步骤质量检测: 进行质量检测,包括尺寸检测、硬度检测、超声波探伤等,确保钢辊符合设计要求。宁河区制造轴
橡胶辊中枢原理:6. 防滑与抓地力 防滑:橡胶表面提供良好防滑性能,确保材料传送稳定。通州区压延轴
主轴的制造工艺直接决定了其性能、精度和可靠性,涉及材料科学、精密加工、热处理、装配技术等多个领域。以下是主轴制造的重要工艺环节及关键技术解析:一、材料选择与预处理基材选取合金钢(如42CrMo、GCr15):适用于通用机械主轴,具有高尚度、耐磨性,需调质处理(硬度HRC28-32)。不锈钢(如440C、17-4PH):用于yi疗、食品行业主轴,耐腐蚀且易清洁。陶瓷/碳纤维复合材料:超高速主轴(>100,000RPM)采用陶瓷(氮化硅Si3N4)或碳纤维增强材料,降低惯性并提升热稳定性。毛坯成型精密锻造:通过模锻或等温锻造祛除内部缺陷,提升材料致密度(密度≥³)。粉末冶金:用于复杂形状主轴(如内冷孔结构),减少后续加工量。二、重要加工工艺精密车削与磨削粗加工:数控车床初步成型,留。精磨削:使用CBN砂轮(立方氮化硼)进行外圆、内孔磨削,尺寸精度达IT4级(公差±1μm),表面粗糙度Ra≤μm。超精加工:电解磨削或磁流变抛光,用于光学/半导体主轴表面镜面处理(Ra<μm)。热处理与表面强化整体调质:淬火+高温回火,提升综合力学性能(抗拉强度≥1000MPa)。表面处理:渗氮:增加表面硬度(HV1000-1200)和耐磨性,适用于齿轮传动主轴。PVD涂层。 通州区压延轴
文章来源地址: http://jxjxysb.fzpgjgsb.chanpin818.com/bzsb/qtbzsb/deta_28746196.html
免责声明: 本页面所展现的信息及其他相关推荐信息,均来源于其对应的用户,本网对此不承担任何保证责任。如涉及作品内容、 版权和其他问题,请及时与本网联系,我们将核实后进行删除,本网站对此声明具有最终解释权。