5.按材料分类金属轴碳钢:45钢(通用)、Q235(轻载)。合金钢:40Cr、20CrMnTi(高尚、耐磨)。不锈钢:304、316(耐腐蚀,食品或化工设备)。铸铁:HT250(复杂形状,如机床床身)。非金属轴应用:尼龙、碳纤维(轻载、防腐蚀,如无人机桨轴)。6.按用途分类主轴特点:机床的重要旋转部件(如车床主轴)。偏心轴应用:产生往复运动(如振动筛、冲床)。凸轮轴作用:操控气门开闭(如汽车发动机凸轮轴)。花键轴特点:带花键齿,传递大扭矩(如变速箱输入轴)。7.按支承方式分类固定轴特点:两端固定,不旋转(如自行车前轮轴)。旋转轴特点:支承旋转部件(如电机转子轴)。总结轴的分类需结合具体设计需求,例如:高转速场景:优先选用合金钢阶梯轴。腐蚀环境:选择不锈钢或非金属轴。空间受限:柔性软轴更合适。实际应用中,可能需综合多种分类特点进行优化设计。橡胶辊制作流程步骤:2.金属芯处理表面处理:对金属芯进行喷砂、清洗等处理,确保表面清洁。通州区压延轴
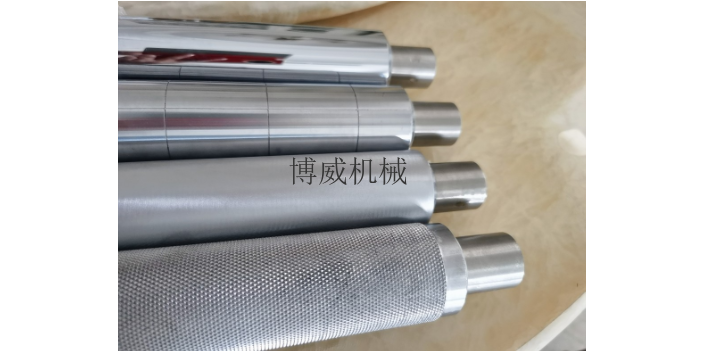
5.现代主轴的重要功能与定义经过长期演变,“主轴”一词已特指机械系统中承担以下重要任务的旋转轴:动力传输:将电机或发动机的动力传递至执行部件(如刀ju、工件)。精密定wei:通过轴承和操控系统实现高精度旋转(如纳米级加工)。承载复合载荷:同时承受扭矩、弯矩、轴向力及振动。6.未来趋势:智能化与绿色制造智能主轴:集成传感器实时监测温度、振动、负载,通过AI优化加工参数。超高速加工:碳纤维复合材料主轴、低温冷却技术突破转速极限。可持续设计:轻量化、低能耗主轴减少资源消耗。总结:主轴演进的逻辑主轴的演变本质是人类对旋转动力操控的不断升级:从人力驱动(陶轮)到自然力驱动(水车),再到蒸汽/电力驱动;从木质粗加工到金属精密化,终实现智能化操控;每一次技术革新(如轴承、材料、数控)都推动了主轴性能的跨越。如今,主轴已成为高尚制造、机器人、新能源汽车等领域的重要部件,其发展史堪称一部浓缩的“机械文明进化史”。 南开区磨砂轴涂布辊带来的便利5. 环bao与安全 减少污染:精确涂布减少涂料挥发和废弃物,降低环境污染。
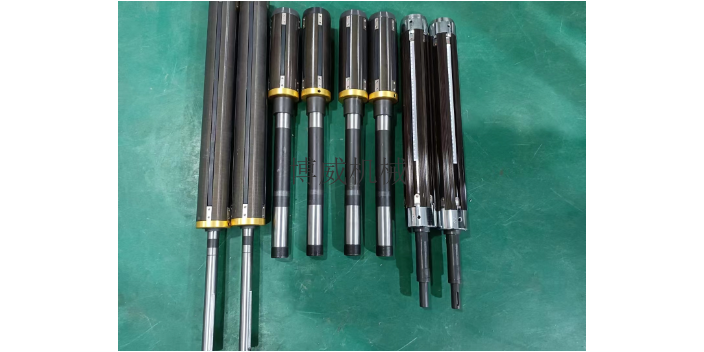
矫直辊轴作为金属板材加工设备中的重要部件,其技术革新与应用对机械设备行业的影响深远,主要体现在以下几个方面:一、提升加工精度与效率,推动高尚制造发展高精度加工需求满足矫直辊轴通过优化材料(如氮化处理、碳纤维增强陶瓷)和制造工艺(如强li旋轧技术),明显提升了金属板材的平整度与精度。例如,灵璧县研发的全球首台1000吨盘轴件碾轧成型设备,通过超细晶改性技术使轴承钢的碳化物细化,接触疲劳寿命提升数倍,加工精度达到纳米级6。这种技术进步直接支持了航空航天、新能源汽车等领域对高精度零部件的需求,例如五轴数控机床在复杂零件加工中的应用,一次装夹即可完成多工序加工,效率提升30%以上8。智能化与数字化升级矫直辊轴的智能化监控系统(如物联网传感器、AI算法)可实时监测轴承温度和振动,预测维护周期,减少yi外停机。例如,宝武钢铁通过此类技术将停机率降低75%1。同时,数控系统的数字化孪生技术(如西门子SINUMERIKONE)使加工过程虚拟化调试成为可能,缩短设备上市时间8。二、促进设备高尚化与国产替代打破高尚技术依赖过去我国高尚矫直辊轴及配套轴承长期依赖进口,但近年技术突破明显。例如。
4.现代自动化与精密操控(20世纪后期至今)大型化与高速化:轧机尺寸和轧制速度大幅提升(如宽带钢轧机速度可达30米/秒),支撑辊需承受更高载荷,其动态平衡、热变形操控成为设计重点。智能化升级:液压弯辊技术、在线磨辊装置的应用,使支撑辊能实时调整辊形,配合计算机自动操控(AGC系统),确保板材厚度公差达到微米级。关键驱动因素总结工业需求:从铁路时代到汽车、航空航天,材料加工精度要求不断提升。力学理论发展:弹性力学分析帮助优化支撑辊的尺寸和布置方式。材料科学进步:新型合金和热处理工艺增强了支撑辊的承载能力与寿命。协同创新:轧机整体设计(如连轧机组)与支撑辊技术的相互促进。现代支撑辊的延伸应用如今的支撑辊不仅用于金属轧制,还扩展到造纸、塑料薄膜等行业的高精度压延设备中,成为工业精密制造的重要组件之一。其演变历程体现了从“被动承压”到“主动调控”的技术跃迁。 钢辊制作步骤7. 装配 组装: 安装轴承、密封件等配件。
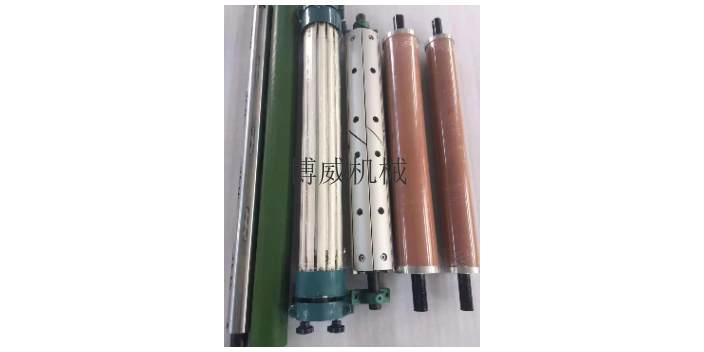
主轴作为机械设备中的重要旋转部件,宽泛应用于多个行业及设备中,其高精度、高转速及稳定性特点使其成为现代制造业的关键技术支撑。以下是主轴的主要应用机械设备及行业分析:一、机床行业数控机床:主轴是数控机床的重要部件,用于驱动刀ju或工件旋转,实现高精度切削、铣削、钻孔等加工。电主轴因高转速(可达数万转/分钟)和高精度,在高尚数控机床中应用宽泛,而机械主轴在中低速、大扭矩场景仍占主导110。车床、磨床、钻床:传统机械主轴因其结构简单、维护方便,宽泛应用于普通车床、磨床的加工环节14。自动换刀机床:配备自动换刀系统的主轴(如SycoTec电主轴)可实现刀ju快su切换,明显提升汽车零部件、模具等复杂工件的加工效率6。二、汽车制造发动机与变速器加工:主轴用于加工发动机缸体、曲轴、齿轮等高精度部件,自动换刀主轴在流水线中提高生产效率69。新能源汽车电池组件:主轴用于电池盖板、电机壳体的精密加工,满足轻量化与高精度需求610。 印刷辊制造工艺7. 表面处理与修饰 抛光:表面进一步抛光,达到所需光洁度。通州区压延轴
印刷辊优势体现3. gao效生产 优势:印刷辊能够高速运转,提升生产效率。通州区压延轴
以下是扎辊轴(轧辊)的主要缺点,结合材料、设计、工艺及使用场景进行分类列举:一、材料与制造工艺缺陷高成本与长周期传统金属轧辊(如合金钢、铸铁)制造需多次热处理(调质、淬火、镀铬等),生产周期长达数月,且高精度轧辊单支成本可达50-200万元36。复合材质(如碳化钨涂层)虽提升寿命,但加工难度大,易出现裂纹等缺陷36。镀铬工艺的局限性传统镀铬层薄(≤),齿顶与齿根镀层不均匀,易导致脱镀、崩齿,降低表面光洁度,增加维护成本3。焊接结构yin患早期轧辊采用焊接连接(如钢芯包胶辊),易形成焊缝缺陷,过载时焊缝开裂,导致皮带断裂或辊轴失效2。二、结构与设计不足重量与惯性问题传统金属轧辊自重较大(如不锈钢辊密度是碳纤维辊的5倍),惯性大,限制转速提升,增加启停能耗12。大型轧辊(如热轧辊)重量可达百吨级,对轴承和传动系统负载压力明显6。密封与润滑设计缺陷轴承座密封设计不合理(如橡胶绳密封),易导致润滑油泄漏、冷却水渗入。油气润滑系统油量操控困难,过量污染环境,不足则润滑失效5。安装与配合问题轧辊与轴承座配合间隙大,或安装同心度偏差,易引发振动、偏载,加速轴承磨损48。 通州区压延轴
文章来源地址: http://jxjxysb.fzpgjgsb.chanpin818.com/bzsb/qtbzsb/deta_28773269.html
免责声明: 本页面所展现的信息及其他相关推荐信息,均来源于其对应的用户,本网对此不承担任何保证责任。如涉及作品内容、 版权和其他问题,请及时与本网联系,我们将核实后进行删除,本网站对此声明具有最终解释权。