传感器故障光电传感器受污染:光电传感器的发射端和接收端如果被灰尘、油污等污染物覆盖,会影响光线的传输和接收,导致传感器误判或无法正常工作。例如,在裁切机中,用于检测物料位置的光电传感器被污染后,可能会错误地认为物料未到位,从而无法启动裁切动作。接近传感器损坏:接近传感器在长期使用后,内部的电子元件可能会因过热、过电压等原因损坏。当接近传感器损坏时,无法准确检测到物体的接近,会使裁切机的相关动作无法按预定程序进行,如无法判断裁切刀具是否到达指定位置,进而影响裁切精度和设备的安全性。压力传感器失效:压力传感器用于检测裁切过程中的压力变化,如果出现故障,可能会导致裁切压力不准确。比如压力传感器失效后,可能会使裁切机在裁切过程中施加的压力过大或过小,影响裁切质量,甚至可能损坏刀具或物料。在裁切设备上安装防护门、光幕传感器等防护装置防止发生意外伤害。江西省刀模自动下料裁切机非标定制
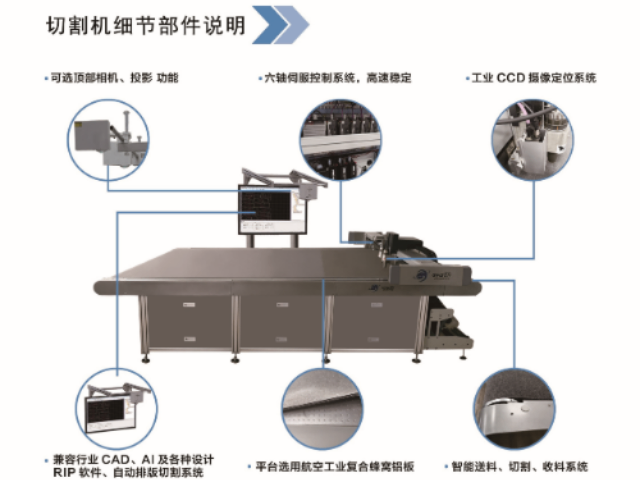
复合材料裁切机的传动系统常见故障有哪些?
链条传动故障链条磨损伸长:链条在运行过程中,链节与链节之间的连接处会因摩擦而磨损,导致链条伸长。链条伸长后会使传动比不准确,链条容易出现跳齿、脱链现象,影响裁切机的正常工作。链条疲劳断裂:长期承受周期性的拉力,链条会产生疲劳裂纹,终导致断裂。链条断裂会使传动中断,造成设备故障。链轮磨损:链轮与链条长期啮合,链轮的齿面会出现磨损,导致链轮齿形改变,与链条的配合变差,容易出现链条打滑、跳齿等问题。 浙江自动裁切机维修裁切机能够根据不同的需求,将泡棉材料裁切成各种形状和厚度的垫片或缓冲条。

改进材料输送系统采用自动送料装置:安装自动送料机,能够将家纺材料连续、稳定地输送到裁切区域,减少人工上料的时间间隔,提高整体裁切效率。优化材料堆放和整理:在上料前,对家纺材料进行整齐堆放和整理,确保材料在输送过程中不会出现卡顿或跑偏现象,保证裁切的连续性。
优化工艺流程提前规划排版:利用专业的排版软件,根据家纺产品的尺寸和形状,对裁切图案进行合理排版,比较大限度地利用材料,减少裁切次数和废料产生,从而提高裁切速度。批量裁切:将相同规格或相似裁切要求的家纺材料集中在一起进行批量裁切,避免频繁更换刀具或调整设备参数,提高设备的使用效率。减少中间环节:简化工艺流程,减少不必要的操作步骤和中间环节,如避免材料在不同工位之间的多次搬运和等待,使裁切过程更加流畅。
选择合适的维修渠道:在传感器出现硬件故障时,首先评估故障的严重程度和自身的维修能力。对于一些简单的故障,可以由经过培训的企业内部维修人员进行维修,以节省外部维修服务的费用。对于较复杂的故障,在选择外部维修服务时,要多比较不同维修机构的价格和服务质量,选择性价比高的维修商。修复而非直接更换:对于一些非关键部件损坏的传感器,在条件允许的情况下,可以尝试进行修复而不是直接更换整个传感器。例如,对于传感器的外壳破裂或一些简单的电路连接问题,可以通过焊接、更换外壳等方式进行修复,这样可以节省购买新传感器的费用。自动化的裁切过程减少了人工操作的时间和工作量,能够快速、提高生产效率,降低生产成本。
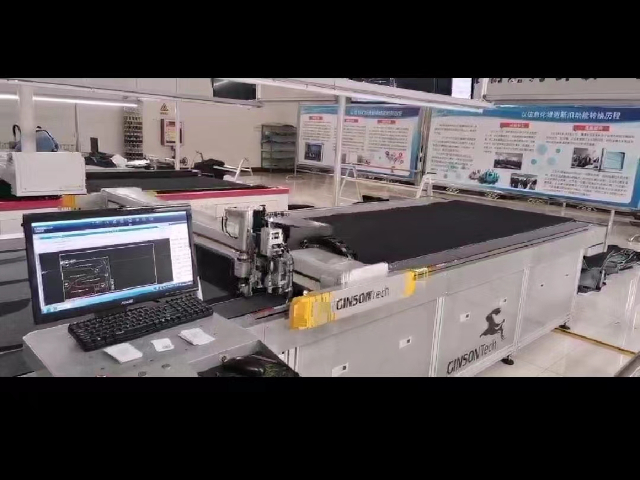
电机本体故障绕组问题用万用表测量三相绕组阻值(三相电机)是否平衡,单相电机需测量主绕组、副绕组阻值是否符合标称值。若出现短路(阻值趋近于 0)或断路(阻值无穷大),需拆开电机修复或更换绕组。检查绕组绝缘层是否破损,可用兆欧表测量绕组对地绝缘电阻(应≥0.5MΩ),绝缘不良时需重新浸漆或更换电机。机械卡阻手动转动电机轴,检查是否存在轴承卡死、转子扫膛(转子与定子摩擦)或传动部件卡死(如皮带轮、联轴器锁死)。若轴承卡死,需更换轴承;若扫膛,可能因电机装配不当或转子变形,需重新装配或更换电机。如使用夹具、真空吸附等,以防止材料在裁切过程中移动或变形。浙江地垫裁切机教程
在电子设备组装完成后,需要贴上各种标签,如产品型号、规格、生产日期、条形码等。江西省刀模自动下料裁切机非标定制
电气控制系统通过各组成部分的协同工作,实现了对复合材料裁切机的自动化控制,确保设备能够按照预设的要求精确、高效地完成裁切任务,同时还具备故障诊断、安全保护等功能,提高了设备的可靠性和安全性电气线路电源线路:为整个电气控制系统提供电力,包括将外部电源引入设备,并通过变压器、稳压器等装置将电源转换为适合各电气部件使用的电压等级。同时,电源线路还配备有熔断器、断路器等保护装置,以防止电路过载、短路等故障引发安全事故。控制线路:连接控制、输入输出设备、驱动装置和传感器等各个部件,传输各种控制信号和数据。控制线路通常采用屏蔽电缆,以减少电磁干扰,保证信号传输的稳定性和准确性。江西省刀模自动下料裁切机非标定制
文章来源地址: http://jxjxysb.fzpgjgsb.chanpin818.com/fzjsb/fqsb/deta_28842279.html
免责声明: 本页面所展现的信息及其他相关推荐信息,均来源于其对应的用户,本网对此不承担任何保证责任。如涉及作品内容、 版权和其他问题,请及时与本网联系,我们将核实后进行删除,本网站对此声明具有最终解释权。